Exploiting Shock Wave Interactions in Geometrically Complex and Compositionally Varying Layered Alloy Structures
(Funding: Army Research Office; Faculty: Naresh Thadhani)
We are investigating the interactions of impact-generated shock waves with geometric interfaces and compositionally varying layered alloys undergoing volume-changing phase transitions, with the goal of exploiting their effects on shock disruption and subsequent tension-induced spall failure. Strain rates associated with increasing impact stress reduce the time for dissipative processes during shock compression. Elucidating and controlling the spatiotemporal evolution of dissipative processes and their effects on impact induced spall failure in nano-to-microsecond time scales is challenging, yet essential for the scientific understanding necessary to predict material behavior under high strain rate conditions. Our research aims to address the challenges by (a) investigating shock disruptions caused by volume-changing phase transitions and determining their effects on impact-induced spall failure, and (b) correlation and mapping of the effects of material and geometric complexities influencing phase transitions and spall failure in order to predict material response and design alloy systems and their micro-/meso-scale architecture, resistant to damage under high strain rate conditions.
The project involves plate-impact gas-gun experiments with time-resolved monitoring of shock-induced volume-changing phase transitions, wave interactions with impedance-mismatched interfaces, and their effects on spall failure. High-fidelity multi-probe PDV interferometry of free surface velocity profiles on multiple samples simultaneously impacted under identical conditions is used to capture the effects on shock rise time, peak velocity and duration, spall pullback, and decompression and recompression strain rates. The signatures captured in these profiles correlated with deformation and damage evolution observed using optical/electron microscopy and X-CT characterization of pre- and post-shock soft-recovered impacted samples help to determine the effects of shock wave disruption and phase transformation induced changes on spall strength and damage initiation and growth processes.
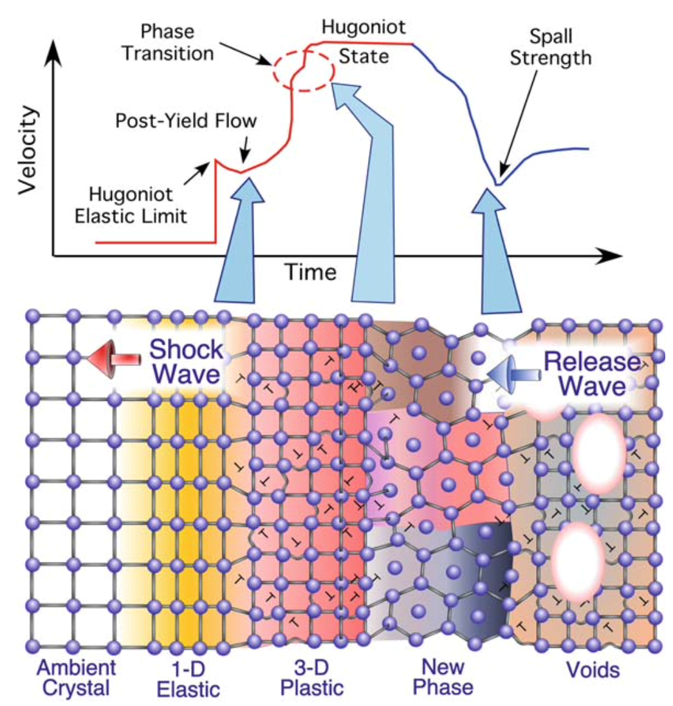
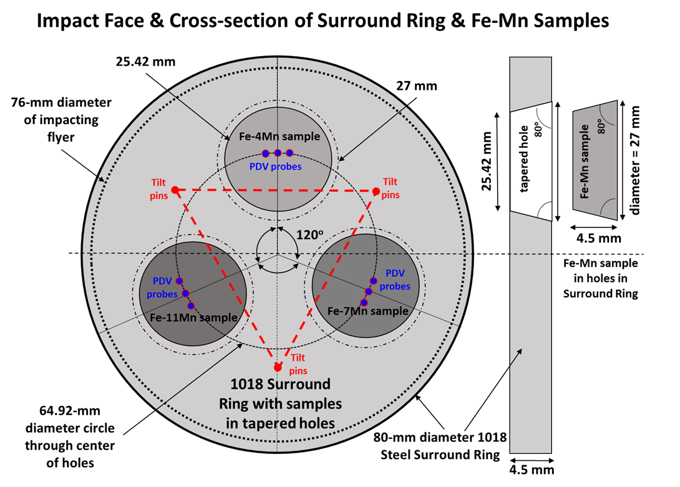